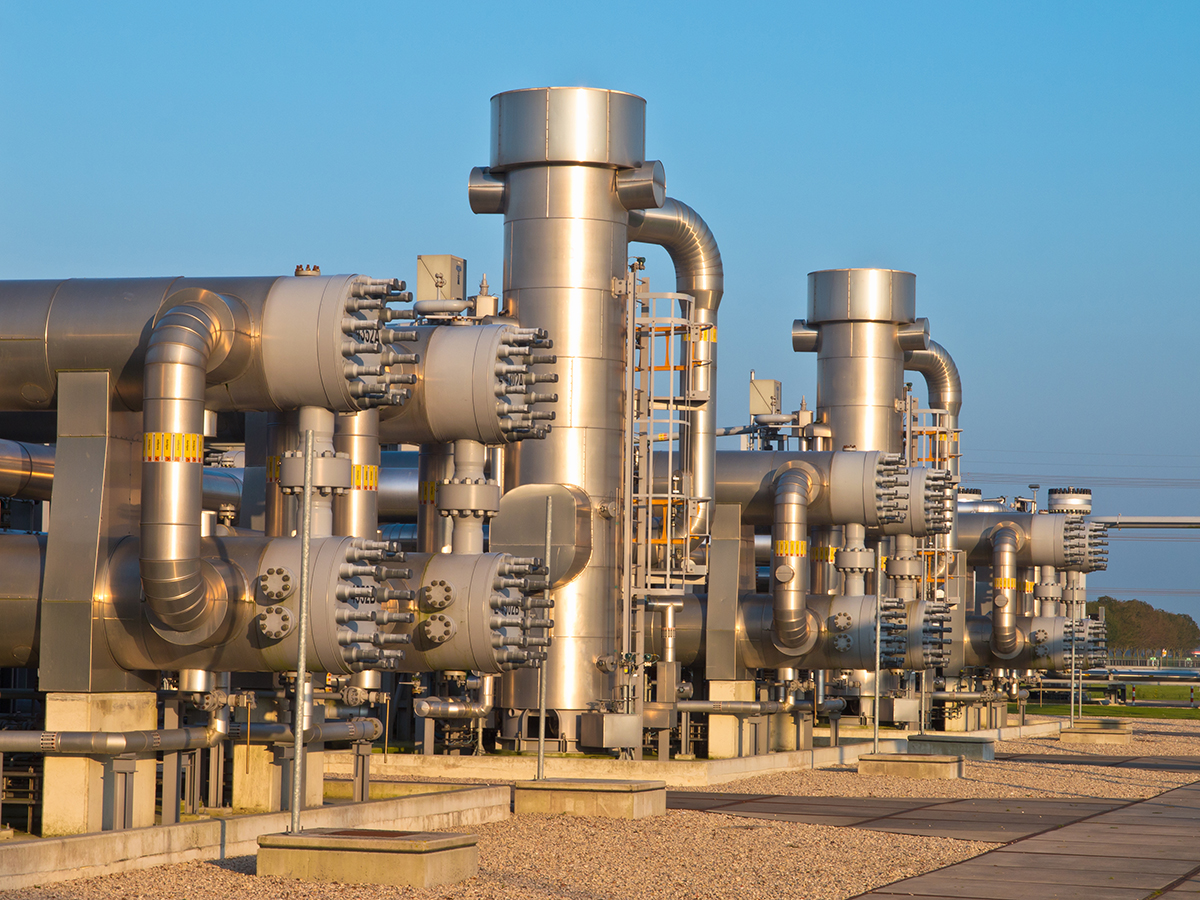
07 Feb Common Hydraulic Problems and the Solutions to It
There are different hydraulic equipment problems that you might be experiencing or is currently being experienced. In this article, we will be listing down the common hydraulic problems. We will also be providing some simple solutions that you can do for your hydraulic oil problem.
These problems may be about hydraulic oil or about the hydraulic equipment itself. But first, we’ll give you a brief introduction on what hydraulic oil is. Hydraulic oil is the medium by which power is transferred in hydraulic machinery. They are commonly used in heavy machine or equipment such as in the marine industry, aircraft, tractors, forklift trucks and more of the like.
Now, here are some of the most common hydraulic problems.
1. Poor Operation
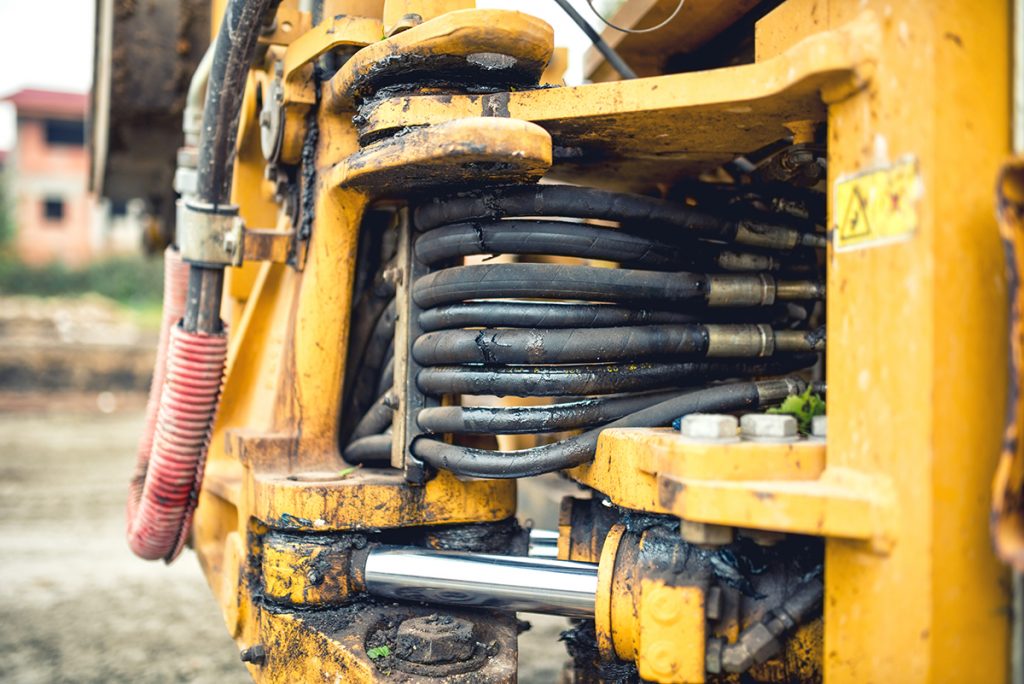
One of the first indications, when there is something wrong with your hydraulic system, is the reduction in machine performance. Loss of speed indicated a loss of flow. This flow can escape from a hydraulic circuit through external or internal leakage.
Leakage is one of the most common causes of a slow operation. There are two types of leakage, internal and external. Internal leakage is when it occurs in the pump, valves or actuators. External leakage is such as burst hoes and is very easy to find.
An infrared monitor is a useful tool to measure leakages and pressure drops. This thermometer can pinpoint potential problems potential problems that you can prevent in the future. A successful infrared test can help pick-up this issue.
2. Abnormal Operative Noise
Abnormal or even irregular sounds while the system is operating are good warning signs of a potential problem that might be occurring or is just about to occur. This abnormal operative noise may be caused by aeration and cavitation.
Aeration is a condition where too much air enters the system and contaminates the hydraulic oil. Cavitation occurs when a hydraulic circuit demands a level of fluid that is too high that what it should be. This makes the circuit pressure fall below the level of vapor in the hydraulic oil.
Check the oil level in the reservoir. If it is low, fill it to the correct level. You may also check the condition of the pump shaft seal and see if it is leaking. If it is leaking, you have to replace it.
3. Unusual High Temperature
This case is caused when the system struggles to correctly evaporate head that could lead to an increase in heat load. This can lead to damage to the seals and in turn, start to degrade the oil itself when the temperature exceeds 180°F or 82°C.
High oil temperature can be caused by anything that either reduces the system’s capacity to evaporate. The reservoir oil level should be monitored and maintained at the right level. Check if there are any barriers to the airflow such as build-ups of dirt. You may also inspect the heat exchanger to dissipate heat. Check the performance of all cooling circuit components and replace it as needed.
We hope that this article has helped you in figuring out what the problems of your hydraulic oil may be. Select the best products for your system in order for smooth operations.
Contact us today and let us help you provide the best hydraulic oil your equipment can have!